The refrigerator runs constantly – how can we fix it?
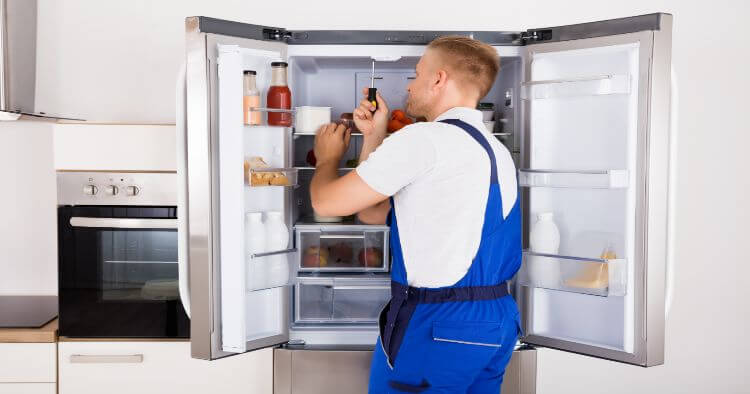
A constantly running refrigerator can disrupt household routines, waste energy, and threaten the quality of your stored foods. Whether you notice excess frost forming in the freezer compartment or unusual changes in temperature, pinpointing the cause is vital. In this blog, we’ll guide you through how to fix a constantly running refrigerator, covering essential steps like cleaning condenser coils, verifying thermostat accuracy, and checking for leaks. By recognizing telltale signs—like frost buildup or a faulty defrost thermostat—and taking timely action, you’ll extend your fridge’s life and restore normal operation.
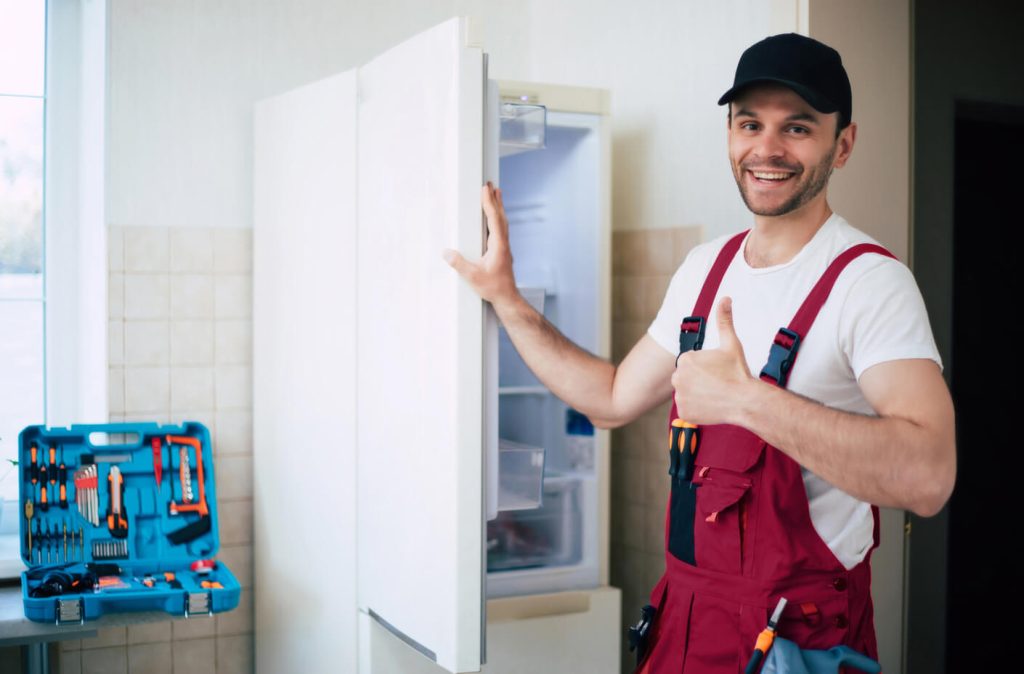
Understand the Defrost Timer, Heater, and Termination Thermostat
A modern refrigerator incorporates defrost cycle components to prevent excessive frost from forming on evaporator coils. This typically consists of:
- Defrost timer or mechanical timer: Initiates the defrost function at intervals to melt ice from coils.
- Defrost heater: Warms the evaporator coils during defrost, removing built-up ice.
- Defrost termination thermostat: A switch that cuts power to the heater once coils reach a certain temperature, preventing overheating.
When these parts fail or misalign, the freezer compartment may accumulate thick ice that never fully melts, causing the fridge to run longer to maintain the correct temperature. A broken or faulty defrost thermostat can also prompt indefinite compressor cycles.
DIY Checks
- Listen for the defrost cycle to start. If your fridge never seems to go silent or switch off, the timer or heater might be stuck.
- Inspect the defrost heater’s glass tube or element for signs of damage or wear.
- Use a multi-meter to confirm continuity if you suspect the mechanical or circuit integrity is compromised.
Any detection of a bad defrost timer or defrost heater tube typically signals the need for either part replacement or thorough assessment of the evaporator area.
Inspect the Door Gaskets for Air Leaks
Why Gaskets Matter
Door seals (aka gaskets) around your refrigerator doors create an airtight boundary that prevents moisture and warm air from penetrating. If these gaskets loosen, tear, or degrade with time, you’ll have a continuous inflow of air, forcing the fridge to work excessively to sustain a constant temperature.
Warning Signs
- Noticeable condensation along door edges
- Minor frost accumulating in corners
- A loose or “sticky” seal that doesn’t sit flush against the fridge’s frame
Fixing
Clean around the seal with warm water and mild soap. If the rubber gasket is cracked or displaying signs of wear, a direct replacement is advisable. A robust seal prevents temperature fluctuations, cutting back on the risk of endless cycling.
Check the Refrigerator and Freezer Door Seals
Closely connected to gaskets, the refrigerator and freezer doors must also close fully for maximum insulation. If your freezer door sags or the fridge door slumps, a gap along the top or bottom can hamper efficient sealing.
- Visual: Observe the door from each angle.
- Paper test: Place a sheet of paper between the fridge and door frame; if it slides out easily, the seal is compromised.
- Realign: Adjust door hinges or fix handle tension. A minor tweak in alignment can restore a tight closure essential for maintaining an even cold environment.
Examine the Condenser Fan Motor for Malfunctions
Role of the Condenser Fan
The condenser fan motor blows air across condenser coils, dissipating heat from the refrigerant. If the motor fails, your fridge’s internal components can overheat, leading the system to run incessantly to meet the demanded cooling load.
Signs of a Fault
- Excess or abnormal noise from behind or beneath the fridge
- Minimal air movement near the coils
- Warm/hot back panel
- The compressor remains active more often than normal
Testing
Unplug the fridge. Access the condenser fan behind the cardboard cover near the bottom. Inspect fan blades for blockages like pet hair or dust. Gently spin the motor shaft to see if it’s jammed. A functional fan should spin smoothly without squeaking. If the motor is seized, a replacement ensures better heat dispersion.
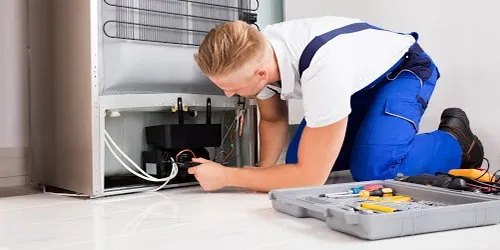
Ensure the Evaporator Fan Motor Is Functional
Evaporator Fan’s Role
Inside the fridge’s interior or behind an evaporator cover, the evaporator fan motor circulates chilled air throughout compartments. If it slows, your fridge won’t reach the correct temperature, triggering lengthier run times.
Self-Check
- Listen for odd or loud noise from the freezer’s back wall.
- Confirm no built-up frost on evaporator coils or around the fan.
- If the fan doesn’t spin consistently, suspect a fault in the motor or the fan blades themselves.
Prolonged issues can degrade overall fridge performance, calling for new fan motor installation and possible defrost checks to ensure ice build-up isn’t jamming the assembly.
Clean the Condenser Coils to Prevent Overheating
Dirty Condenser Coils as a Common Issue
Coils near the fridge’s base or back often accumulate dust, pet hair, and debris. If these dirty condenser coils can’t dissipate heat, the fridge’s motor runs overtime, straining to maintain your desired temperatures.
Simple Steps to Clean
- Unplug the fridge from its power source.
- Use a coil brush or vacuum with a brush attachment to remove surface filth.
- Run the vacuum nozzle gently, ensuring you dislodge any stuck clumps.
- Reconnect power once the area is cleared.
Performing this coil cleaning on a regular basis (like every 6 months) keeps the fridge’s cooling efficient and prevents potential meltdown situations.
Assess the Sealed System for Potential Issues
Key Sealed System Components
The refrigeration system—evaporator tubing, condenser coils, compressor—operates under sealed conditions. If any portion develops tiny punctures, refrigerant might slowly leak, forcing the fridge to run longer:
- Signs of wear or corrosion on metal tubes
- Inconsistent cooling in certain compartments
- Weaker or partial freezing
Professional Approach
Pinpointing a sealed system leak demands advanced knowledge, specialized tools (like leak detectors or multimeter checks for electrical continuity), and sometimes careful soldering. If a “sealed system” fault is confirmed, you may face a major fix or consider a new appliance if repair costs exceed the fridge’s value.
Verify the Temperature Settings of the Refrigerator
Incorrect Temperature Setting
Sometimes, a user inadvertently dials the control panel or mechanical knob to a colder level than recommended, prompting the fridge to remain in “cool mode” beyond normal cycles.
Adjust
- For freezer sections, aim for around 0°F, while the fresh food area typically thrives around 37-38°F.
- Always confirm with your brand’s recommended range in the user manual. Setting it too low often yields an overworked fridge plus possible frost-laden produce.
Test the Thermostat for Accuracy
Thermostat Necessity
A fridge or freezer thermostat, sometimes referred to as a cold control or “thermostat setting,” influences your fridge’s operating cycle. A miscalibrated or faulty one can keep the compressor humming, trying to hit an unreachable target.
Basic Thermostat Check
- Twist the dial or adjust the digital setting. If no change in the fridge’s hum or temperature occurs, suspect a potential short.
- Use a multi-meter to test for continuity in the thermostat wire or the thermostat itself.
- If you detect no continuity at standard operating conditions, it might be time for a replacement.
Look for Obstructions in Airflow
Freezer Vent Issues
Inside many top-freezer or side-by-side refrigerator models, air traveling from the freezer compartment to the fresh-food area can be hindered by items or frost. Overcrowded shelves or large pizza boxes might hamper the air outlet, spurring indefinite cooling cycles.
Proper Organization
Give space between items so that air flows efficiently. Check that stacked containers don’t block the rear vents, and keep the vents free of moisture or ice. This ensures uniform cooling and helps the fridge cycle off as intended.
Inspect the Compressor Operation
Compressor Role
Found behind or beneath your fridge, the compressor motor drives refrigerant across evaporator coils and the rest of the system. If it labors for hours on end, it’s likely responding to false signals or dealing with poor cooling efficiency from other failing parts.
Compressor Problems
- Excessive or constant hum
- Overheating, occasionally felt by warm sides on the fridge exterior
- Physical damage or corroded lines near the motor connections
Because the compressor forms your fridge’s “heart,” a thorough approach—like verifying the condenser fan motor or checking for significant refrigerant leaks—ensures no underlying cause is being missed.
Check the Refrigerant Levels
Low Refrigerant
When refrigerant is partially or heavily depleted, the fridge can’t meet the correct temperature range effectively, causing near-constant running. Possibly from micro leaks or worn connections, refrigerant depletion usually reveals slow performance, inconsistent cooling, or partial freeze areas.
Expert Intervention
Recharging refrigerant is tricky. Attempting to do so without the correct gauges and licensed knowledge can cause more harm or violate local regulations. If repeated recharges are needed, the sealed system might be compromised.
Investigate Potential Electrical Issues
Circuit or Wiring Problems
Occasionally, a miswired or shorted line can keep the fridge in permanent cooling mode:
- Fault in the defrost circuit that never triggers the heater
- Loose or corroded wires near the evaporator fan or thermostat controls
- Overheated or fused relay on the main board
Evaluating electrical parts typically involves referencing a wiring diagram or performing continuity checks with a multimeter to confirm signals, ensuring no partial breaks keep the fridge locked in a continuous run loop.
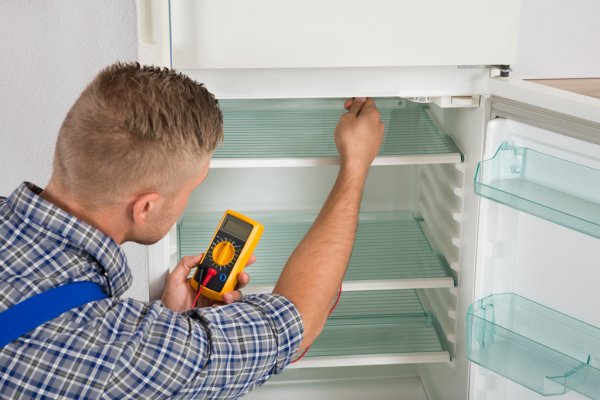
Consider the Age and Efficiency of the Refrigerator
Older Models
Legacy units might have less insulating foam, mechanical defrost timers prone to failure, or worn door gaskets. If you’ve exhausted simpler fixes and the fridge is a decade or more old, upgrading to an ENERGY STAR model can help you avoid constant running and reduce energy bills.
Weigh the Cost
It’s essential to weigh a possible major repair—like replacing a compressor or redoing the sealed system—against the cost of a new fridge. The older the device, the more probable frequent breakdowns hamper everyday life.
Consult the User Manual for Troubleshooting Guidance
Manufacturer Advice
Sometimes, the simplest approach is verifying the recommended settings or steps indicated in your fridge’s user manual. You’ll find:
- Correct temperature ranges for both freezer and fresh food compartments
- Layout diagrams for removing door or evaporator cover
- Quick instructions on adjusting the defrost timer or resetting the control
Reviewing brand-specific guidelines can solve overlooked details, from re-latching a parted defrost cycle to calibrating the fan motor and other internal components.
When to Call Toronto Refrigeration
Toronto Refrigeration stands ready to deliver professional solutions when your fridge refuses to stop running or you’re unsure how to safely handle complex repairs. Our licensed appliance experts excel at diagnosing common and advanced issues across major appliances, from evaporator or condenser coils to defrost circuits. With a wealth of experience in top fridge models—including diagnosing a mechanical defrost timer in older units or pinpointing a failing motor in newer digital systems—our team swiftly restores normal operation. As part of our commitment to customer satisfaction, we blend cost-effective fixes, genuine OEM parts, and thorough aftercare. Whether your fridge has dirty condenser coils, a stalling condenser fan motor, or a suspect heater element, we handle it all—saving you time, stress, and preserving your prized foods.
Conclusion
A fridge that won’t stop running signals deeper mechanical or electrical concerns. By verifying each possibility—from a faulty defrost timer to dirty condenser coils—you can often achieve a simpler fix and keep your fridge humming at the right temperature. Routine cleaning of fans, coils, and door seals stands as crucial maintenance to curb undue stress on your refrigerator. When in doubt, always seek out skilled professionals who provide safe, effective diagnosis and solutions. Proper attention to everything from thermostats to compressor function ensures consistent cooling, protects your foods, and extends your fridge’s lifespan.